
挑战
位于德克萨斯州博格的Nutrien氨厂废热锅炉经常出现管道故障。其蒸汽发生器平均每年发生两次故障,所产生的维修成本和生产损失对该厂财务造成了重大影响。每次停机仅维修就需要花费约$350,000,此外还会导致生产损失。
由Kellogg设计的氨厂产量为1500吨/天 (TPD),需要1500psig的蒸汽来确保涡轮机和压缩机的运转,并为各个工艺阶段加热。该系统通过协调pH磷酸盐程序(又称全效磷酸盐)处理的高纯给水产生520 klb/hr的蒸汽。处理过程的控制对于防止锅炉高热通量区域的腐蚀和酸腐蚀起着至关重要的作用。
协调pH-磷酸盐程序使用两种磷酸盐-苛性碱产品混合物来控制锅炉水的pH值,该pH值可能因氯化物或硫酸盐等杂质的存在而产生波动。蒸汽厂操作员需要经常测试锅炉水的pH值和磷酸盐,以及其他控制指标,并将测试结果输入Veolia基于云的数据管理系统InSight*。该系统使用专有分析来指导操作员调整处理应用。
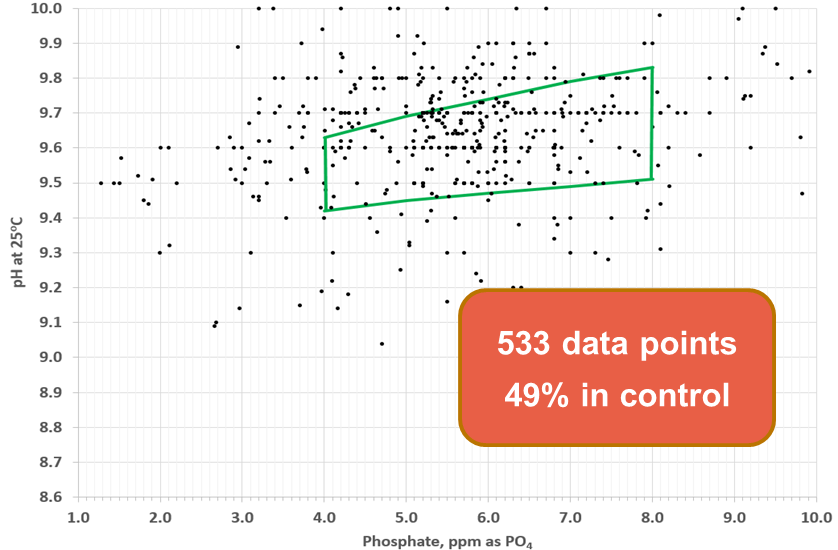
由于给水质量会发生变化,而且处理的应用和控制是通过手动完成的,所以锅炉水的pH值和磷酸盐会不断地在控制限度内外移动。依靠该厂的常规操作,会有超过50%的测量值超出规定限值(图 1),这也解释了锅炉管反复出现故障的原因。 Nutrien博格工厂希望改进对锅炉水pH值和磷酸盐的控制,以降低与锅炉故障相关的成本。
解决方案
Veolia建议该厂使用自动化系统来监测水参数,并将该系统连续地与处理应用直接连接。锅炉精度系统 (BPS) 使用在线pH探针的读数来确定实时应用的磷酸盐产品正确混合(图2)。来自工厂DCS的蒸汽流量信号对化学剂量进行控制,使剂量率与蒸汽产量保持一定比例。通过添加排污流量计,并将化学品进料速率与该读数联系起来,还能进一步改进控制,优化对锅炉进料和排放的控制。博格工厂正在考虑于未来实施这一举措。
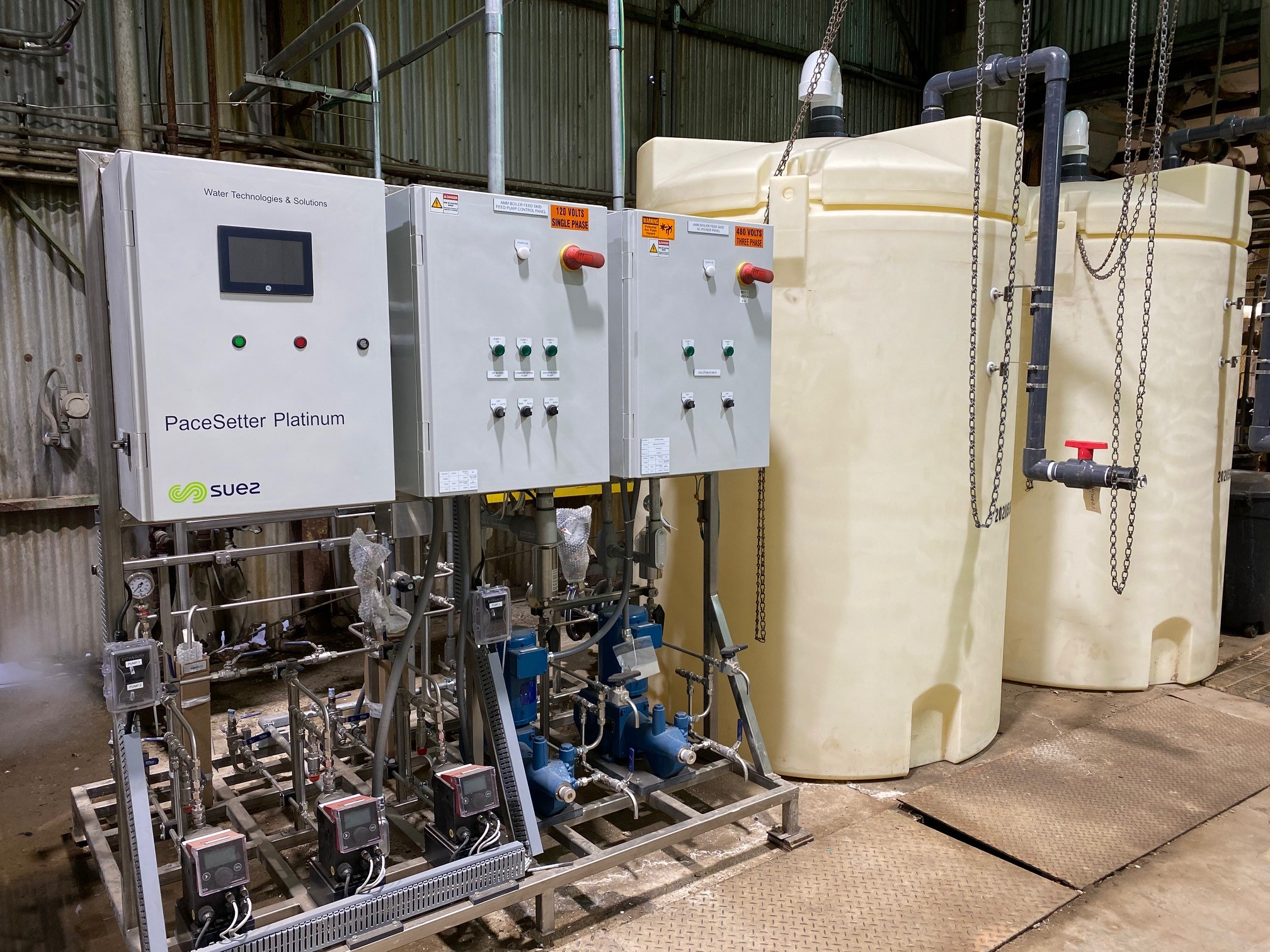
使用自动化学监测和剂量系统可以连续进行测试和调整,而不是像操作员进行实验室测试和手动调整处理那样每天进行几次。
结果
BPS系统投入运行后,该厂锅炉水的pH值和磷酸盐含量随即趋于稳定。在几天时间内就可以看到,该系统显著改善了对处理的控制,超过80%的数据点落在了控制范围之内(图3)。
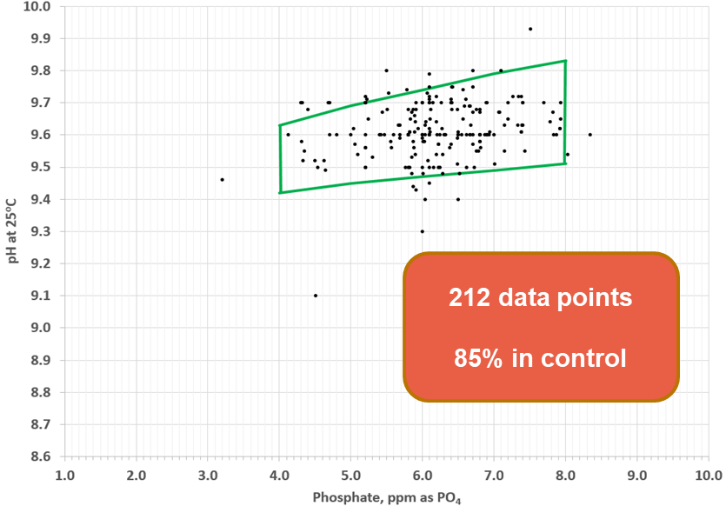
除了连续读数和化学调整外,BPS系统还包含一个样品温度控制单元,可确保pH测量在受控条件下进行,从而缩小误差范围。
由于采用了自动化学品配料系统,操作人员不必频繁地在化学品进料泵和储罐附近工作,降低了与化学品接触相关的安全风险。虽然操作员仍需在每个班次进行测试以验证在线读数,但之前用于配料的时间可用来完成其他增值任务。
“多年来,Veolia一直为我们提供水处理和专家服务,这种合作伙伴关系为我们的公用事业带来了许多改进。锅炉精度系统提高了锅炉的可靠性和化学品应用的安全性,同时也大大减少了计划外停机时间。”
Nutrien博格氨厂主管Mark Marquez
安装BPS后的12个月里,Nutrien博格工厂没有发生过一起锅炉管故障。据估计,该厂每年可减少$275,000的维修成本,其资产寿命也将得到延长。