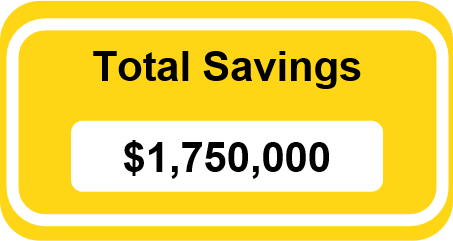
挑战
北美一家生产烯烃的行业领先的化学加工厂运行着两个立式管壳式交换器(A和B),使用锅炉给水和蒸汽冷凝水来带走工艺中的热量。由于这些装置容易受到悬浮铁颗粒的污染,因此采用Millipore过滤分析进行定期测试,以确认装置进水和出水中的铁污染保持在较低水平。
从历史上看,这两种换热器都产生了良好的铁效果,铁含量均低于50 ppb(以Fe计),Veolia技术代表每月都会使用Millipores对其进行测量。再一次停机后,尽管新清洁的换热器已上线,但铁含量仍然很高(图 1-蓝线),因此在运行一年后对其进行了更换和检查。
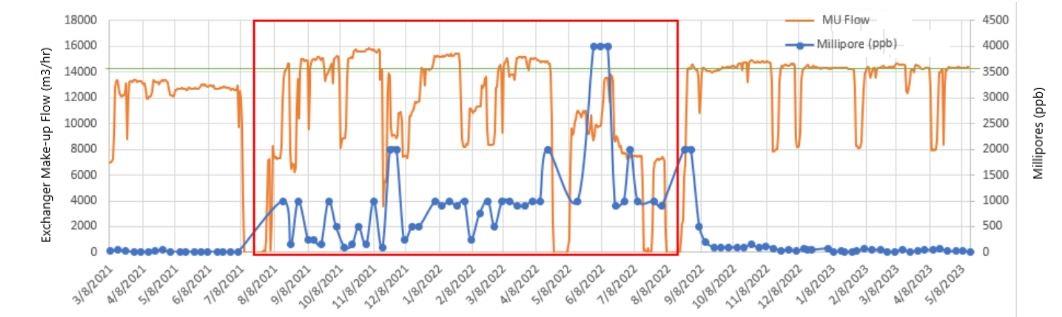
图 1:Iron Millipore 测试显示,当蒸汽负荷达到设计负荷的 120-125%(橙线)时,整个 2021-2022 阶段(蓝线)都显示出较高水平。
解决方案
从中部和底部收集管材样品,并在位于德克萨斯州Tomball的Veolia分析实验室进行冶金分析,在那里观察到金属的细长气刨和点蚀。Veolia还审查了操作方法的变化,并审核了水处理计划,以确保遵循最佳实践方法。通过全面的研究,以了解容器内部的工作原理。
该容器的设计特点给水侧带来了独特的挑战:
1) 该容器没有集成汽包,而是使用挡板。由于没有集成的汽包,这意味着内部液体/蒸汽界面的蒸汽分离空间有限,这使得该区域容易发生腐蚀和沉积。该容器对水位变化也更敏感,导致高排污率,尤其是间歇性排污,这会破坏内部循环并导致低水位警报。
2) 传统锅炉的给水从机组顶部进入,而该锅炉的给水从底部进入,正好位于弯道的上游,导致水循环的方向变化。从该位置进入的较冷锅炉给水可能会造成温度和循环问题。
3)由于挡板的存在,内部水循环路径中的多个180°转弯使得换热器更容易产生微粒氧化铁沉积。此外,如果在超过设计蒸汽负荷的情况下运行,这种几何形状可能容易发生流动加速腐蚀 (FAC) 和/或侵蚀腐蚀。
4) 连续排污和锅炉水采样点位于机组底部附近。最佳做法是在吃水线以下收集连续排污,以便对浓度最高和最具代表性的水进行采样。在设备底部收集的水将显示大量沉淀的固体,可能无法代表水的总体状态。
对管子的金相分析显示,管子底部有细长的气刨和点蚀痕迹,但没有流动加速腐蚀(FAC)的迹象。这可能表明,当交换器的运行超过设计的110%时,容器中存在导致铁损失和/或腐蚀的条件,与流动加速腐蚀无关。这可能是由于高速沸腾时出现异常沸腾状态,或蒸发至干涸,导致腐蚀性盐类沉积。在这种情况下,如果蒸汽负荷超过设计的110%,建议将管壳材料升级为更高级的合金,以提供更多保护。
结果
在查看运行数据后,我们注意到高铁结果与蒸汽负荷之间有很强的相关性,达到设计水平的 120-125%。在之前的运行中,峰值蒸汽负荷达到比设计高出 110-115%(图 1 - 橙色线)。该换热器于6月上线,但秋季不稳定的工况让Millipore的测试结果并不可靠。9 月后,随着工厂运行趋于稳定,并开始试验将换热器中的蒸汽负荷保持在设计的 120% 以下,铁含量趋于稳定并最终下降。Millipore表明从样品中获得的铁含量较高,但不能确定铁污染的来源。
为确保停机后投入使用的热交换器处于最佳启动状态,该工厂开发了离线清洁和钝化程序。
在对换热器进行操作调整后,蒸汽负荷现在控制在设计的最大 110%,Millipores 已恢复正常并继续跟踪。由于换热器的故障会导致至少3天的停机时间,以及更换或重装换热器的额外费用,因此节省的费用估计为1,750,000美元。
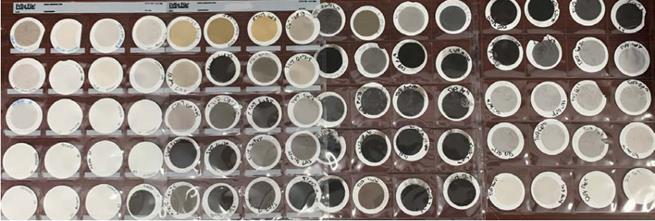
图2:Millipore结果显示,在将负荷降低到120%以下后,铁含量呈上升趋势和下降趋势