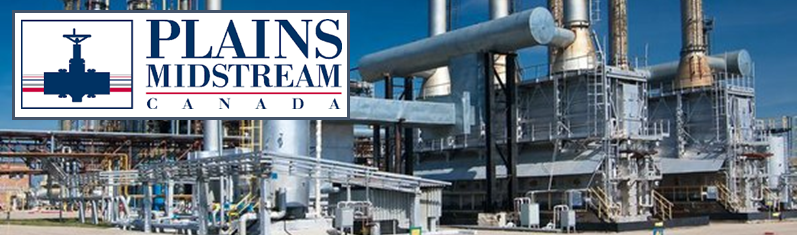

Plains Midstream是位于阿尔伯塔省南部的一家天然气厂,该厂废水处理设施的磷酸盐排放受到限制。Veolia提供的解决方案采取了可减少磷酸盐排放、碳排放以及水和化学品消耗的措施,有效解决了该厂所面临的问题。这些改变使该厂的年度总节约金额达到$51,850。
Veolia建议将锅炉处理过渡为全聚合物Solus AP化学品。这种新型处理方法可防止之前所遇到的锅炉沉积现象。
这种新的处理策略还能更好地控制锅炉浓缩循环,优化燃料、水和化学品的使用。
整个北美乃至全世界每一个行业的公司都在努力减少对环境的影响,同时优化生产效率和控制运行成本。
自1970年以来,磷酸盐一直作为控制沉积的标准锅炉处理方法。而现在,磷酸盐正逐步被性能更强、对环境影响更小的全聚合物溶液所取代。
使用磷酸盐化学成分的锅炉往往会产生淤泥,因而无法保证最佳传热表面的清洁度,妨碍了锅炉循环倍数的优化。当锅炉给水得到浓缩或“循环提高”时,排污量会相应减少,进而降低了水和能源的使用。
鉴于环境排放许可的变化迫在眉睫,减少客户污水处理系统的磷酸盐 (PO4) 负荷是十分必要的。
最大的挑战在于,有一定比例的锅炉排污水会含有高达20 ppm的PO4,而有时候由于其中一个锅炉的排污池位置和KlarAid*除磷酸盐处理的化学品进料位置问题,这些污水会在未进行除磷酸盐处理的情况下传送至废水处理系统当中。这会导致工厂的废水中出现磷酸盐超标和排放许可超标的风险更高。图1为废水处理系统示意图。
想要纠正这种情况,选择十分有限,其中包括将锅炉排污池改道连接到KlarAid注射液的上游,这样,所有进入排污系统的水都能得到处理,而这种方案涉及到复杂而昂贵的结构改造。Veolia建议将锅炉内部处理的化学成分改为Solus AP,这是一种新型的无磷酸盐锅炉处理方案。
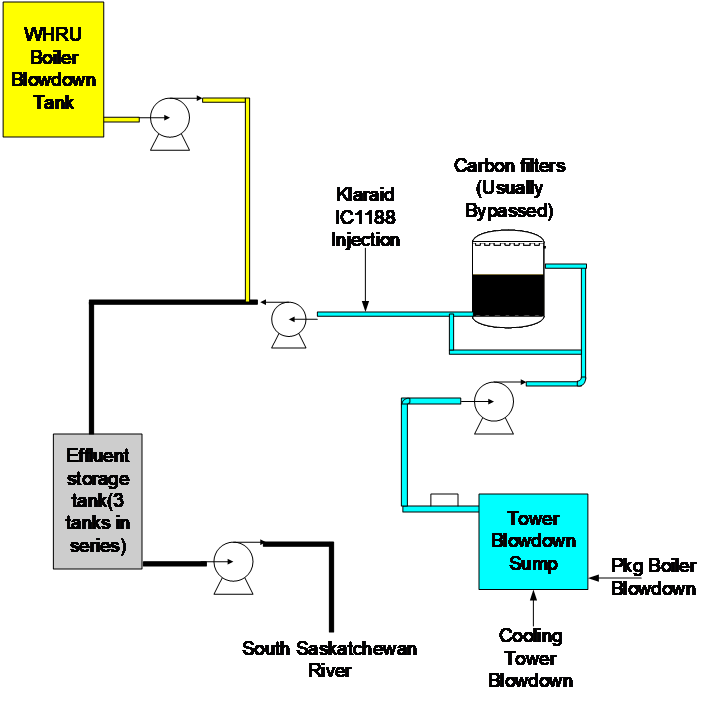
图1:废水流示意图。
改变内部处理的化学成分,也为改善锅炉浓缩循环控制提供了机会。新的处理策略设定了一个剂量方案,使操作人员更容易对循环倍数进行优化,减少耗水量,并降低现场一台快装锅炉和两台余热回收锅炉 (WHRB) 的燃料消耗。
Veolia推荐使用的Solus AP是一种新一代锅炉内部处理剂,使用的是获得专利的锅炉三元共聚物 (BTP)。BTP是一种多功能聚合物,它通过将进入的给水污染物(如钙、镁硬度)保持在可溶解状态,使其有效地排出到锅炉排污池,有效限制了沉积物的形成。BTP的作用还包括扭曲晶体生长以减少形成颗粒的大小,改变悬浮颗粒和锅炉管表面的电荷,减少颗粒与颗粒之间的吸引力,以及它们对锅炉管壁的吸引力。
由于硬度离子等污染物的存在,基于磷酸盐的方案被称作“沉淀方案”,这种方法需要有效去除所形成的污泥,否则其自身也会成为沉积物的来源。我们强烈建议使用Solus全聚合物方案,因为该厂曾有过硬度超标的历史,这使得磷酸盐污泥管理成为了一项额外挑战。
从2019年3月起,Solus AP处理取代了原有的磷酸盐沉淀方案,并采用了为期8周的启动程序来过渡内部处理的化学成分。新的处理策略以70-80个浓缩循环为目标,是以前锅炉运行的两倍。由于该工厂无法用流量计和控制器跟踪水力循环,使用准确的剂量方法和监测有助于增加锅炉的循环倍数,从而节省能源、水和化学品的消耗。
结果
由于过渡到了Solus AP,锅炉的浓缩循环从平均40次增加至75次。随着锅炉水浓度的增加,排出的经化学处理过的热水减少,使得未经处理过的冷锅炉给水也相应减少。
锅炉循环倍数的增加,使得每年可节省用水1百万美制加仑,节省价值$9,777的燃料,并节省价值$18,977的锅炉处理化学品。所节约的燃料相当于每年减少CO2排放量200吨。
补充水的减少,也带来了与工厂脱盐器操作相关的节约。随着锅炉循环倍数的增加,脱盐厂每年需要对其共流阳离子与阴离子装置进行再生的次数减少了52次,节省了价值$11,246美元的酸和苛性钠。
通过取消基于磷酸盐的锅炉处理方案,污水厂的磷酸盐负荷每年减少200公斤PO4。这一改变降低了Klaraid处理的使用量,使得每年用于去除磷酸盐的花费降低至$11,846,且更重要的是,将以PO4形式排放的磷酸盐浓度减少了1 ppm,消除了工厂排放许可超标的风险。